top of page

PLASTIC INJECTION MOULDING SOLUTIONS
Have your vision made to exacting standards with our integrated in-house manufacturing service. Start at any point in the process, or choose our full-service option.
Certification
ISO 9001
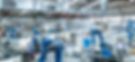

CAPABILITIES OVERVIEW

INJECTION MOULDING
-
26 Injection Moulding machines – Toyo and Krauss Maffei
-
30T to 450T Clamp
-
Integrated 6 axis robotics
-
24/7 production
-
Aspect PL/Microsoft Dynamics MES/ERP
-
Insert Moulding
-
Overmoulding
-
On-site Toolmaking Facility

POST PROCESSING
-
Pad Printing
-
Assembly
-
ISO Class 7 Cleanroom
-
Annealing

QUALITY
-
Quality Management System - ISO 9001
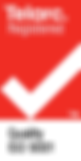
Capabilities Oveview




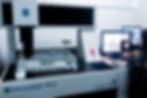



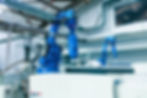

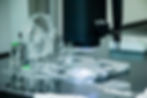

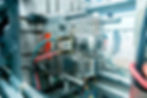





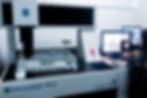



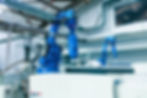

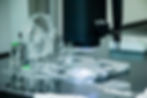

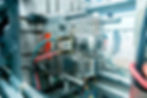


bottom of page